在這個雪茄菸盒大小的神祕空間裡,居然躲進如此多神秘且高度智慧的技術,而且在這些魔力施展下,就能夠讓我們開車獲得精準且生動的指引,即便在森林裡也不用丟麵包屑做記號,不管到哪裡都不會迷路。但是這些導航機究竟怎麼生產出來?有多少繁雜的程序等著擔任Garmin生產線工程人員的我們前去嘗試?實際操作後,所有環節皆讓我們恍然大悟。
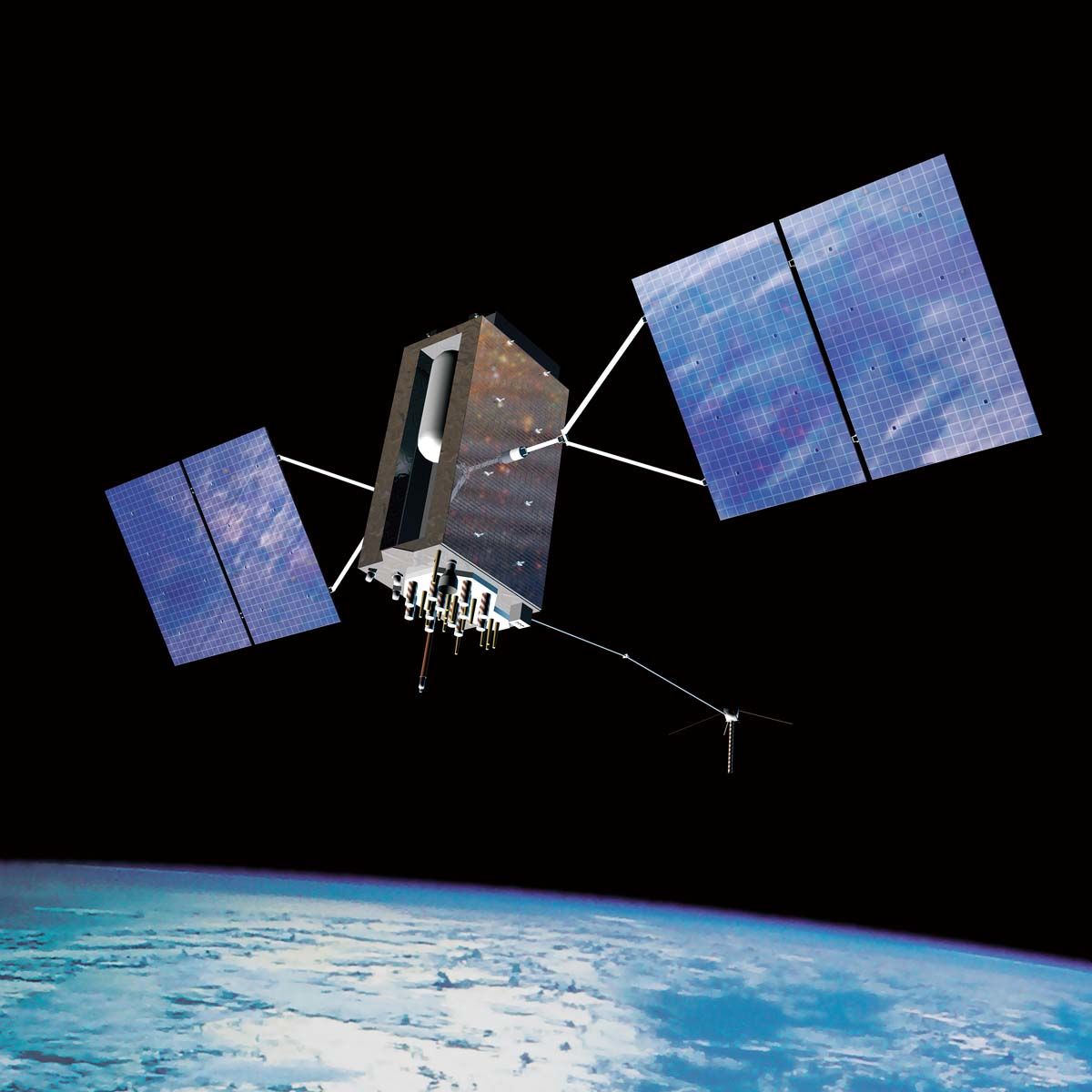 |
文賴震宇 / 圖廖子賢、Garmin / 協力廠商Garmin / 設計 徐信平 十多年前車用衛星導航在國內市場開始成為開車族出門必備武器,過去靠著傳統地圖和問路方式前往目的地的模式正式揮別我們的生活,結合語音指引和彩色螢幕顯示介面讓我們輕鬆就可以獲得精準的街道圖資,找到朋友家的門牌早就不需經過數不清的鬼擋牆便可輕易達成。儘管經過科技的演化,傳統導航機的領域逐漸被結合導航功能的車用主機及智慧型手機所侵蝕,進而演化出同時具備導航、行車紀錄器和衛星電視甚至於胎壓偵測器等多元化的導航機,單一功能導航機已經不吃香,但導航系統對我們來說,永遠是相當重要的一部分。 |
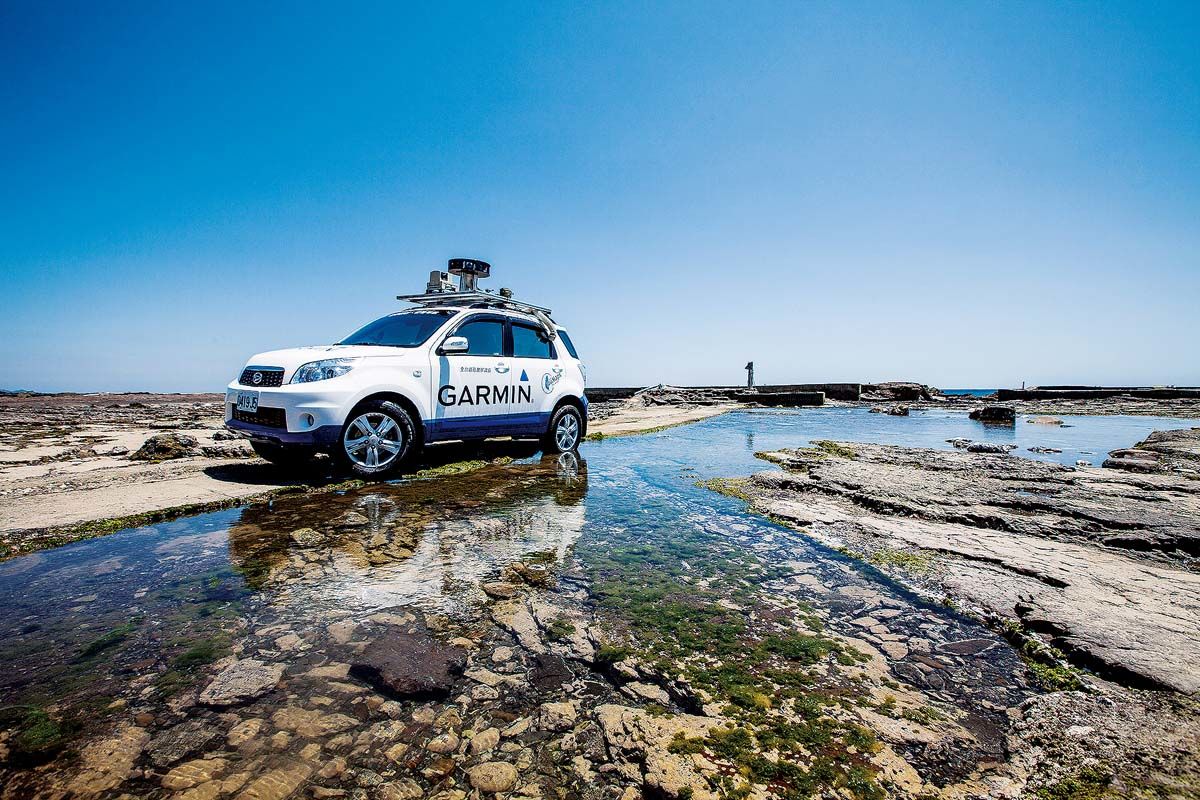 |
Garmin在全台灣的幾部路調車翻山越嶺走過國內各個角落,不論是拍攝的街景或者是荒郊野嶺的圖片最終都送進後製中心建檔儲存,以作為地理資料和街景繪製的來源。 衛星導航從何發展而來 我們生活中有不少東西都源自於軍用技術,例如微波爐最早的概念是從美軍雷達設備而來、數位相機起源於航太領域、電子計算機的誕生主要是現代戰爭導彈路線的運算,仰賴GPS衛星定位的民用導航同樣也是如此。上個世紀1970年代由美國國防部三軍聯合研發出來的第一代軍用衛星導航定位系統,其功能主要可提供陸海空軍即時且全天候的導航圖資,如此軍隊在進行軍事行動時就不會迷失方向,迅速找到集合地點及攻擊位置。1993年耗費超過300億美元的GPS正式建構完成,美國政府也將衛星定位系統由軍方獨佔逐漸開放給民間使用,並且在2000年取消對民用訊號的干擾,經過多年發展,民用版的GPS不僅準確度愈來愈高,同時多年來也衍生出極具規模的相關產業,並提供龐大的就業機會。 |
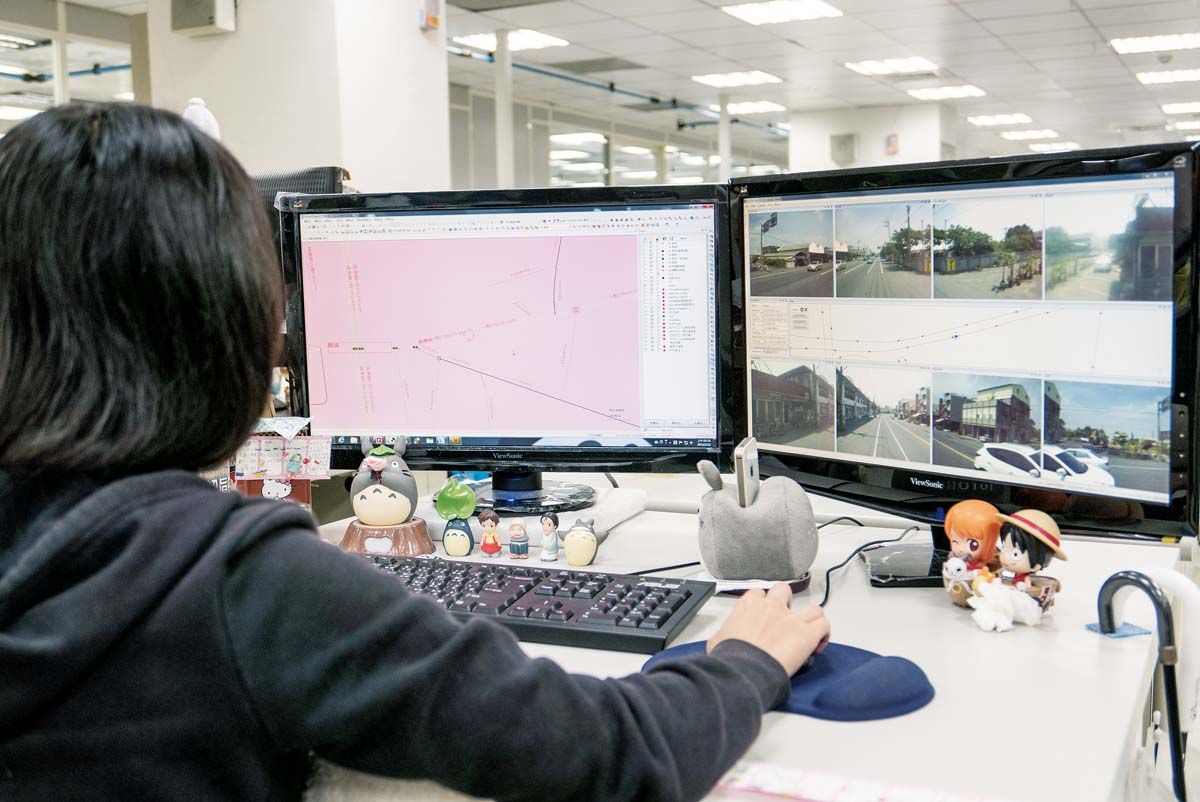 |
後製人員將拍攝的街景與描繪的地圖網路相結合,同時在街道路線上完整結合設計出各種建築和地標物等圖案。 PART 1. 導航的靈魂 圖資與電路板設計 過去曾經用了那麼多年的導航機,但從來沒有拆卸開來了解內部構造,甚至進一步了解導航機透過怎樣的設計達成運作的消費者,或許跟我一樣對導航機盒裡的秘密很有興趣,此次透過全球導航機市佔率龍頭的Garmin邀請,終於得償所願一窺這大型現代化工廠重重戒備的禁區,直搗黃龍直接坐在生產線旁擔任生產人員參與產品製造過程。 如同一般中大型國內電子廠一樣,Garmin之所以要嚴密控制進出人員就是為了保護商業機密,因此若非事前經過行銷部邀約並通報門口警衛登記參訪單位及人員姓名,這輩子你大概別想有機會闖進去,不過也由於多數研發和生產屬於專利技術範圍,因此之後的各項介紹也顯得格外小心,部分細節無法透過鏡頭公諸於世。在接待人員介紹下,我們大致了解目前Garmin在導航領域所生產的產品類別,之後很快就直接進入生產的核心,見識一下最基本的圖資資料如何製作。 |
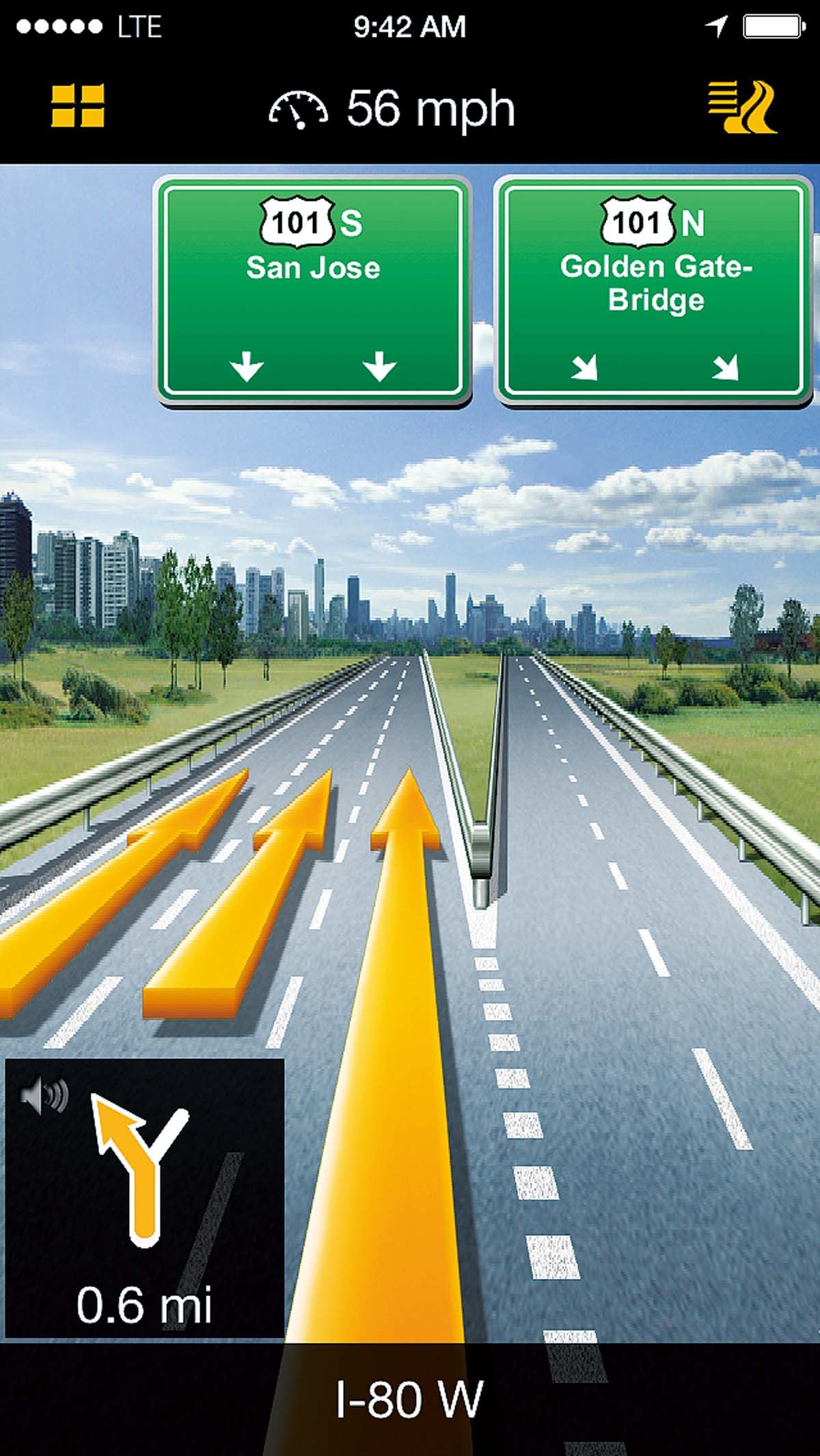 |
除了透過量測獲得精準的路線外,好的導航畫面呈現也需要美編人員以美觀且淺而易懂的設計手法創造出來。 將環景圖片轉化為地圖資訊 在實際將顯示螢幕、接收器和電路板等零件送上生產線組裝以前,我們還是先看看導航機上的地圖是如何繪製的,這些最重要的靈魂最終在輸入導航機的記憶體後,一部衛星導航才能正常運作。通常在路調車以車頂上八部相機組合成360度攝影後將街景記錄成照片,這些圖片最後經過後製中心的美編逐一比對建檔,再繪製成你所看到的導航機地圖畫面。由於Garmin的圖資和相關應用軟體皆自行製作,因此我們可以看到整間後製中心坐著一群人數龐大的後製人員,隨時在為街景、路線和地形地物的圖資更新進行繪製工作。 |
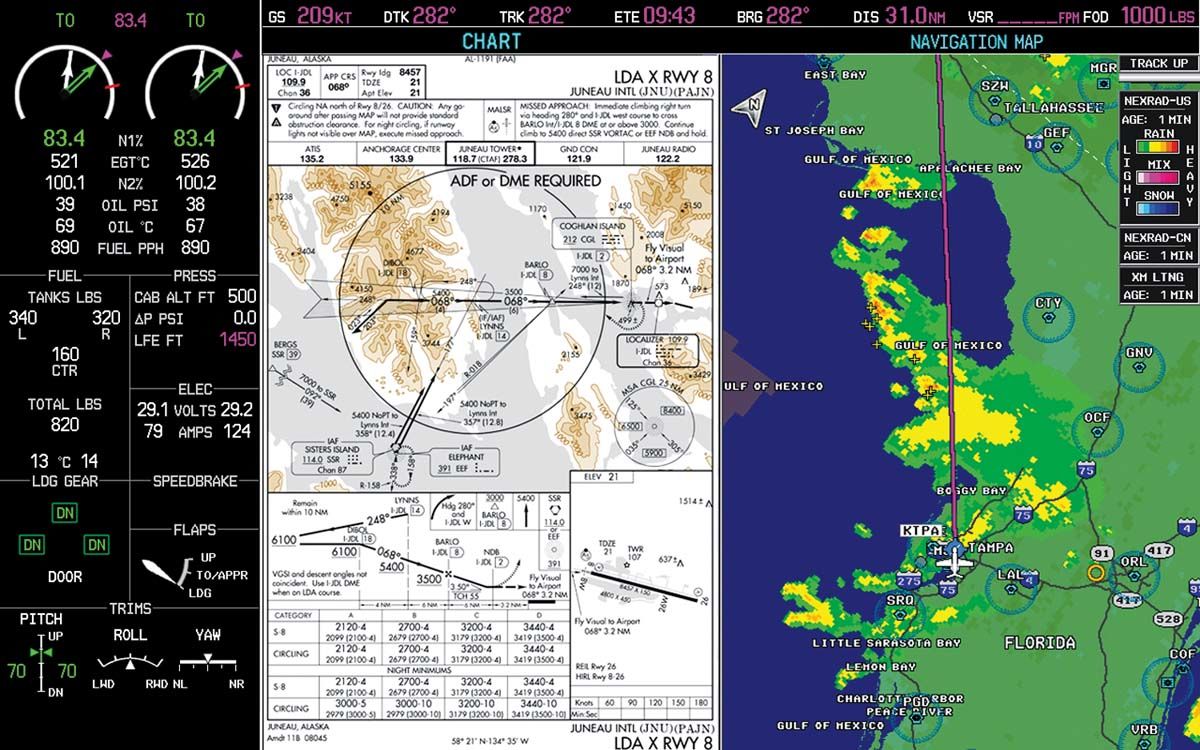 |
航空導航地圖資料則是利用空中攝影和空中測量技術,最後將攝影圖片、向量圖層疊合起來。 通常電子地圖的內容除了以一般市區街道和各種公路網絡為基礎外,還包括了其他重要地標,如建築物、鐵路、橋樑、各政府機關、地下道、醫療和休閒場所等,後製人員的工作除了要將這些物件詳盡的畫出來外,同時還得轉換為圖像鮮豔且淺顯易懂的圖案,並將各複雜路口的路網利用3D建模的技術將實景數位化;不過除了街道畫面構成外,完整的地圖資訊還需要藉由GIS地理資訊系統將圖形資料的向量結構利用AutoCad等製圖軟體將空間中的點、線、面結合起來表現空間資料,這個部分屬於難度頗高的專業領域,從沒上過專業設計製圖軟體課程的我們,光是看到這些複雜的測量地形圖資料轉化成的GIS圖層就已經頭皮發麻,更不用說是把這些圖層疊合在一起,最後得以與接收的GPS衛星定位訊號相結合,成為我們每天在使用的導航系統。 |
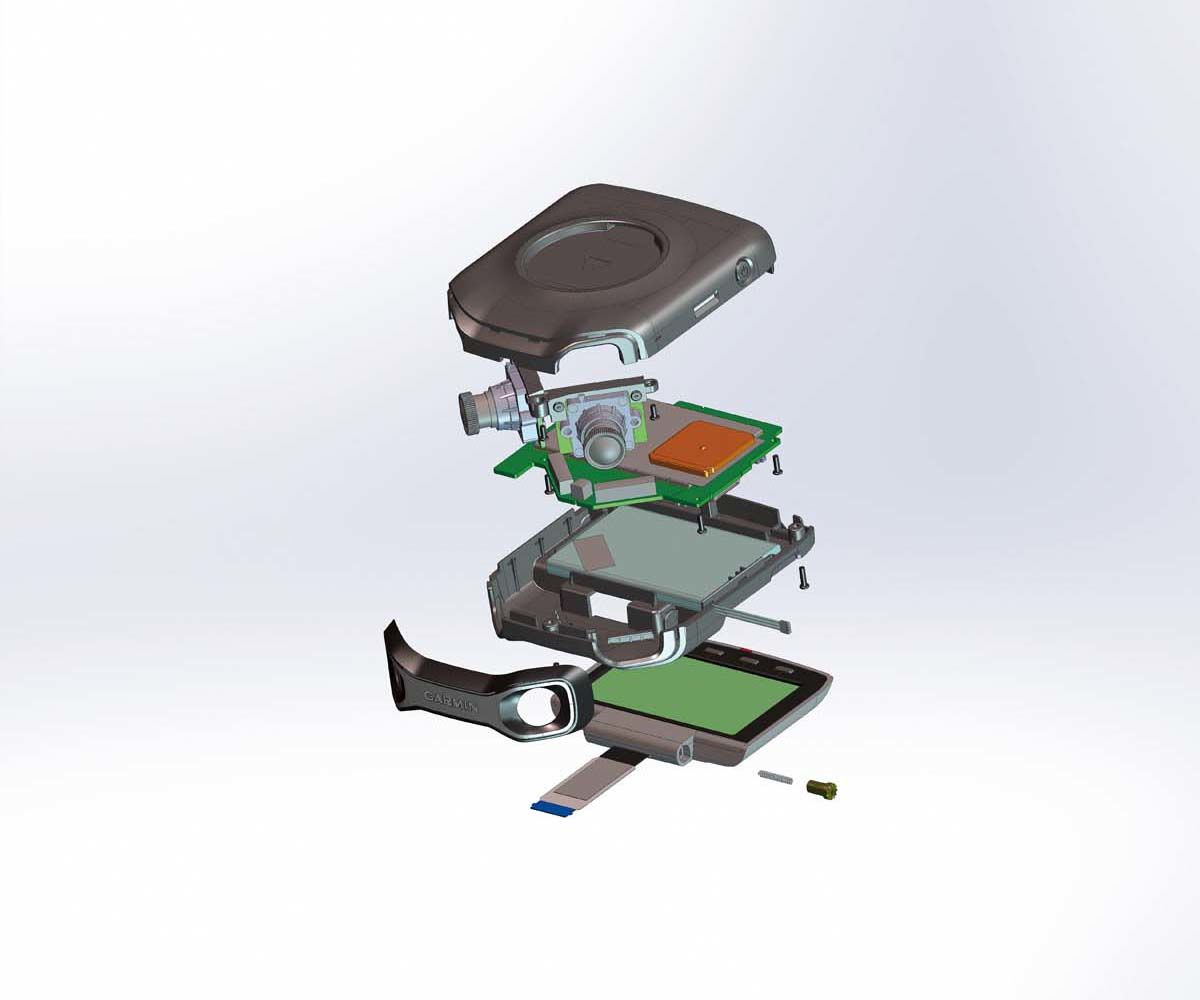 |
除了導航機外,Garmin早就將程式編寫專業、鏡頭技術、顯示螢幕加工改良等相結合,生產像GDR 190機型的行車紀錄器提供200度水平高廣角影像紀錄功能。 |
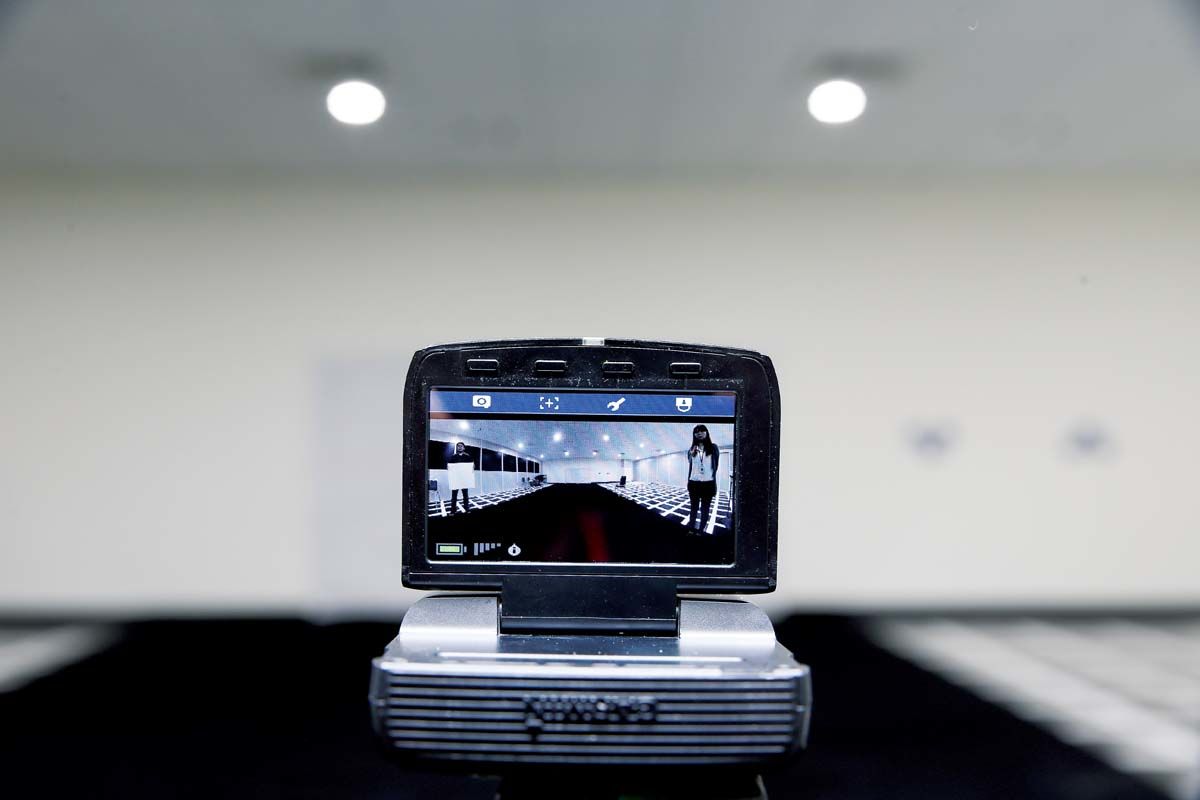 |
透過軟體讓電路板設計更迅速 通常研發部門會先行設計電路板圖,最後委外印刷。因為電路板設計攸關導航機各項功能如電源開關、GPS的接收、觸控螢幕的顯示,事前設計便至關重要,因此工程師會先以PCB(Printed Circuit Board)印刷電路板設計軟體進行設計。PCB設計最難的地方,就在於目前電子商品功能愈來愈複雜,因此印刷電路板PCB上頭的零件和線路變愈來愈密集,設計工作也就顯得更具挑戰性。 |
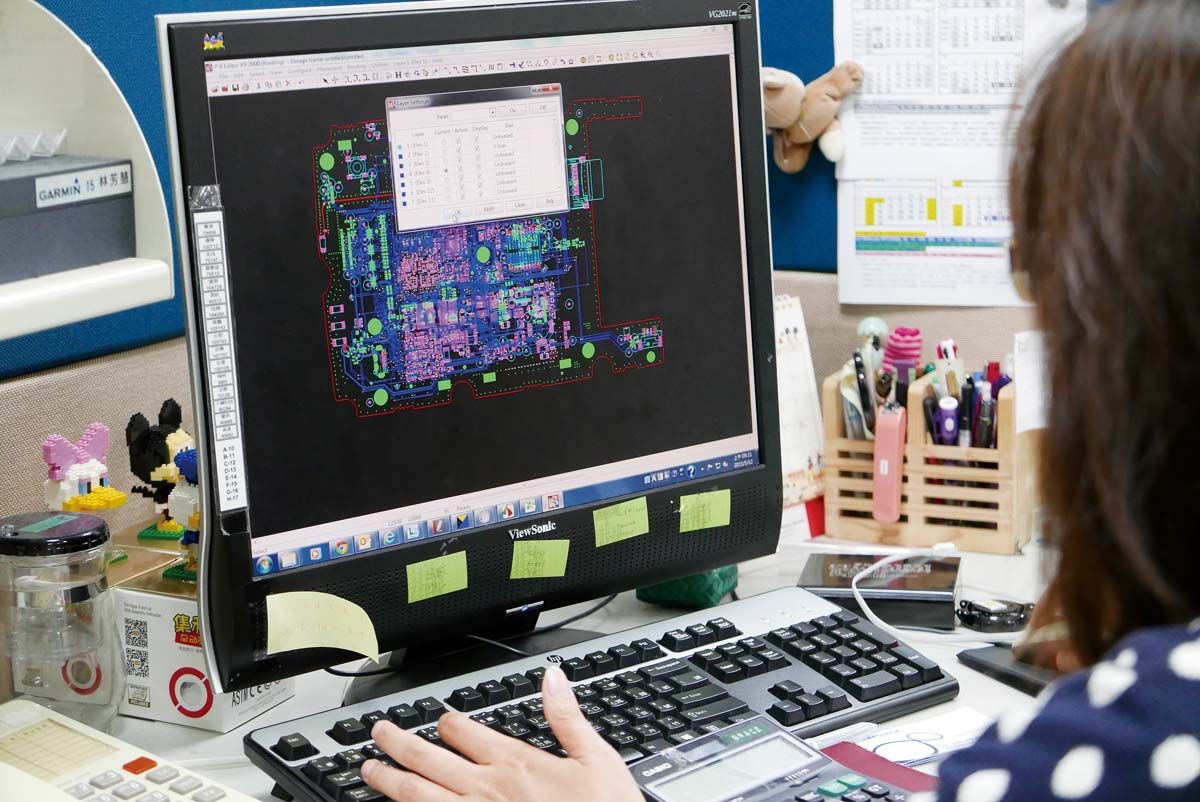 |
透過軟體,工程師很容易就可以掌握電路板的佈線規劃,處理電路規則,解決串擾限制、線路斜限制和屏蔽問題。 在設計PCB之前,我們必須先準備SCH電路原理圖文件和PCB電路板圖文件,通常PCB電路板圖文件的難度較高,因為它攸關電路板實際安裝的所有布局,SCH(Schematic)文件則只需注意各種管座和管腳的屬性標註和對應即可。之後就來到PCB的結構設計,在事先確定好的電路板尺寸下透過PCB設計軟體繪製板面,預留佈線區域和非佈線區域,並依照設計需求安排所有插接零件、開關、螺絲孔和安裝孔等,之後就是PCB上各種零件的佈建,在SCH原理圖和PCB電路板圖上導入元件網絡,所有需要的零件就可以按正確位置分佈在上面。 其實整個電路板設計最複雜的地方就在於佈線的安排,另外目前最新的佈線平台,負責設計的工程人員得以在自動和手動佈線間彈性變換,各式佈線工具也變得較容易設定和管理,對於高密度佈線區域內的設計,可以節省不少設計人員的時間。 |
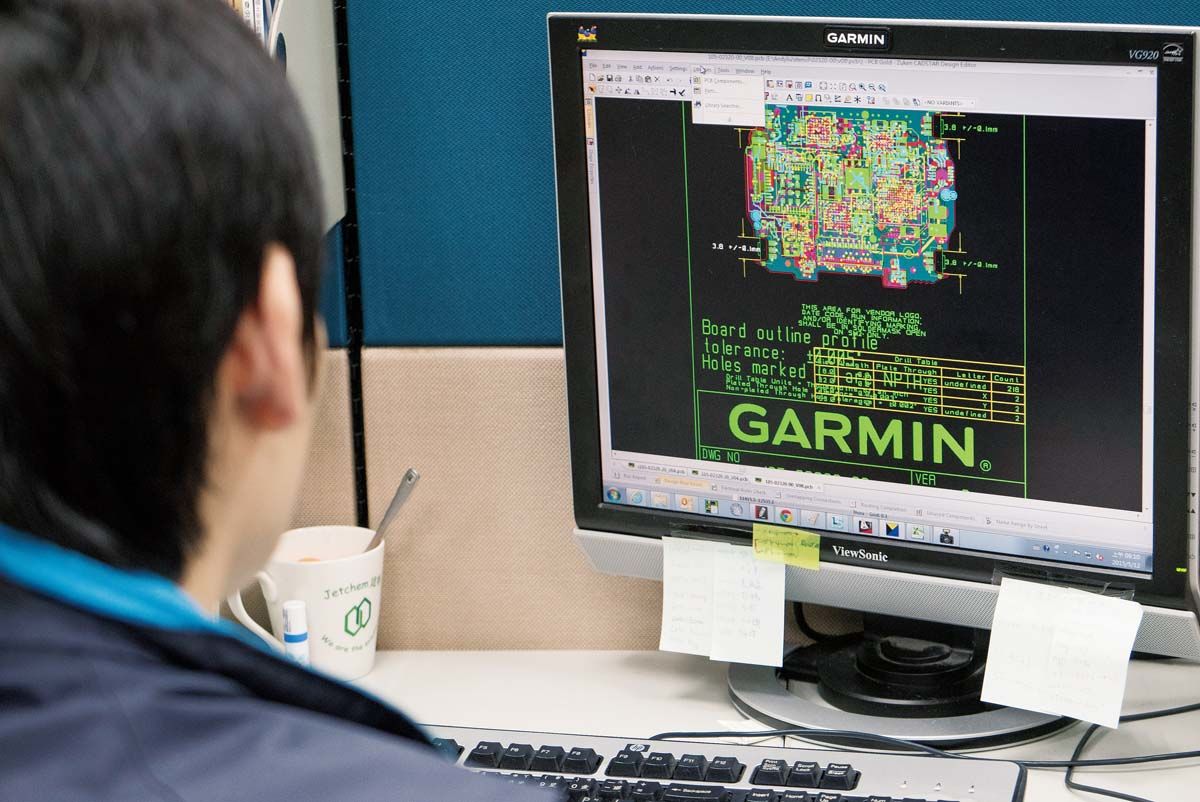 |
在PCB電路板設計時,設計者會依照產品所訂的尺寸,透過設計軟體繪製板面,預留佈線區域和非佈線區域,並依照設計需求安排所有零件。 SMD固態電容裝配 在經歷圖資製作和PCB電路板設計工作流程之後,負責生產線的主管便帶領我們先去員工餐廳吃午餐,暫時先將工作擺一旁了,而中午12點的「放飯鐘」一響,所有生產線人員暫時離開工作崗位,享受一個半小時的用膳和午休時間。 經過先前極度專業的工作環境洗禮之後,原以為下午的工廠生產流程只有組裝那麼簡單,似乎在一個多小時的想像後又覺得自己錯了!是不是連組裝控管都那麼難,其實後來實際體驗之後,頂多就只是流程多了點,動作並不複雜,真正複雜的其實是一關關的挑出不良品及產品品質背後可怕的高度要求,以及非門外漢的我們所能快速領悟的專業知識。 |
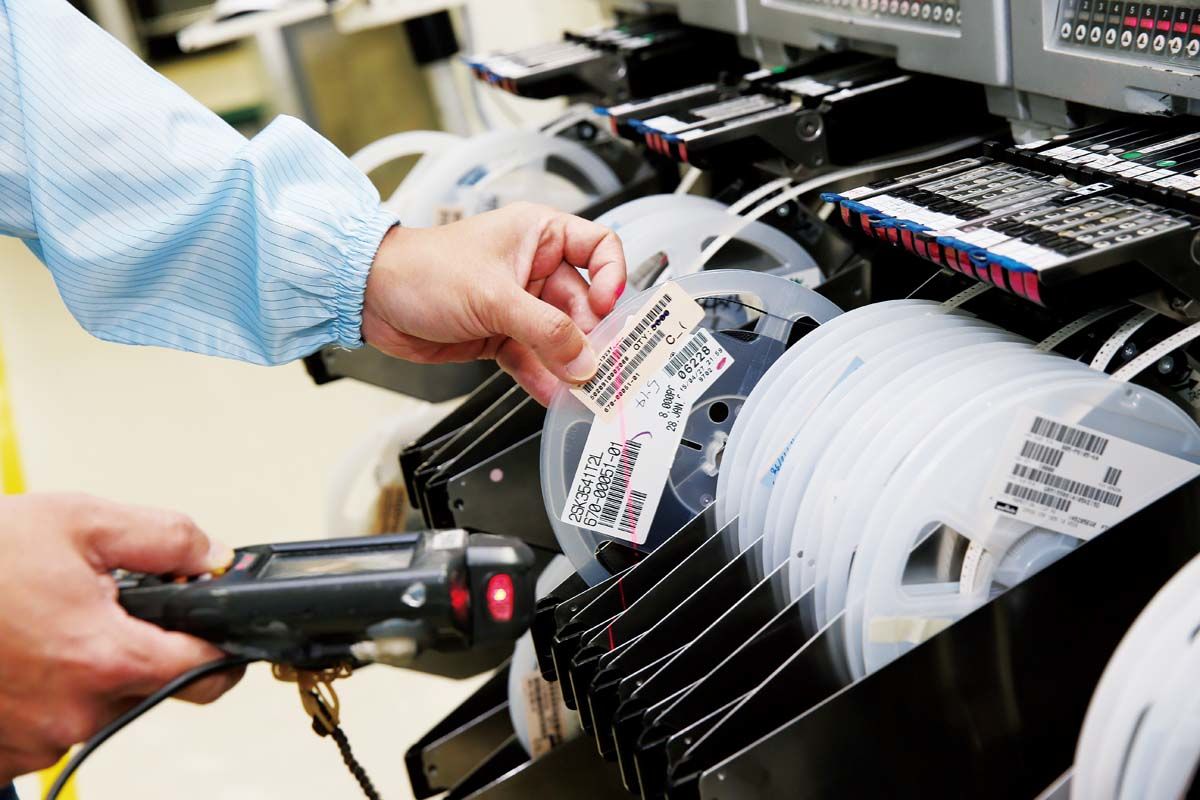 |
在印刷電路板進入SMD生產設備後,生產人員必須為每件PCB進行編號並加以核對,有了可以辨識的零件編號,才能夠確保生產流程各關品質監督並在發現故障品時抓出錯誤環節。 在印刷電路板PCB經過高科技的SMD(Surface Mount Device)固態電容生產設備後,基本上所有電阻和電容會依照當初設計圖安排的位置以錫膏焊接在上面,但是如果機器偶爾出錯呢?第一關就將電阻電容焊錯位置或者是焊接效果不良造成問題,後頭不就全盤皆錯!別怕,這一關還有我們同時擔當品管測試人員為SMD裝配線把關,為電路板上各項組件的安裝進行校準和檢查。檢測人員先以顯微鏡檢查經過SMD後的電路板上各項零件安裝是否定位以及銲錫狀況外,接著再連線透過電腦來檢測電壓和電流是否正常,若所有功能都正常,就可以進入下一個流程。 |
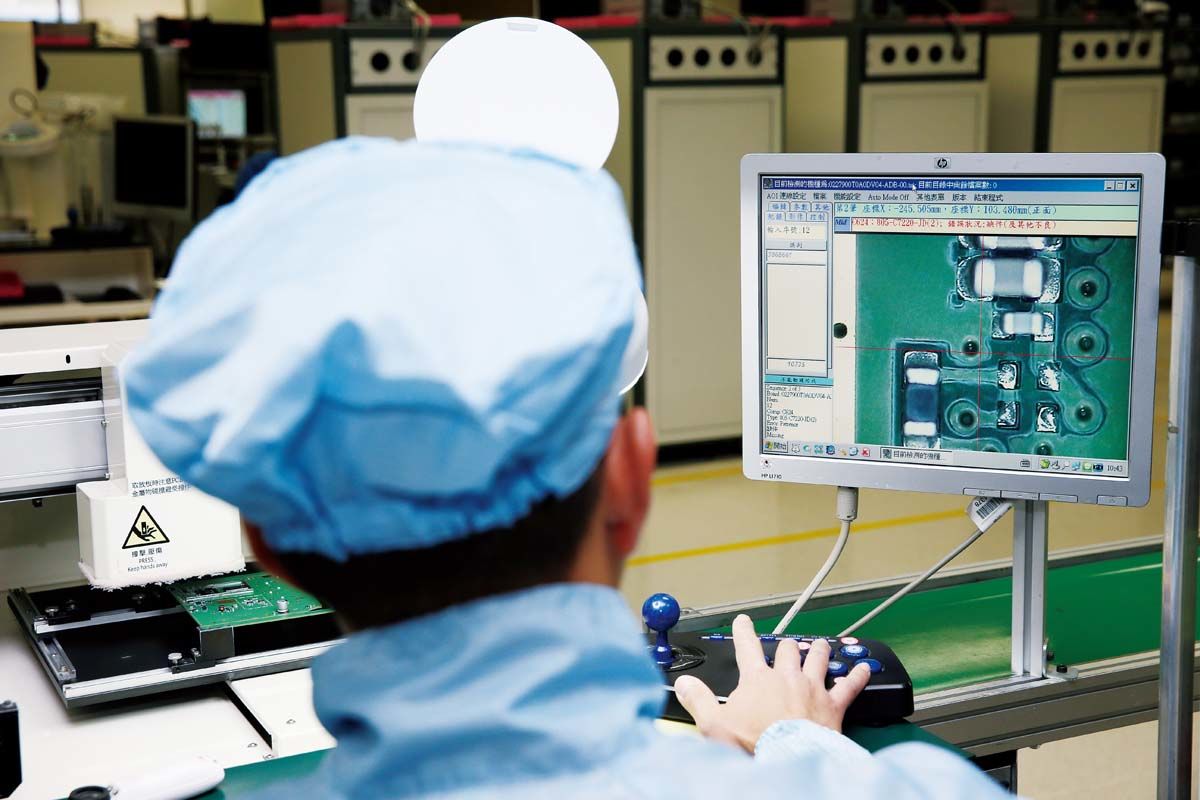 |
經過SMD處理後,檢測人員透過顯微放大仔細查看電路板上有無任何焊接瑕疵或組件錯誤。 |
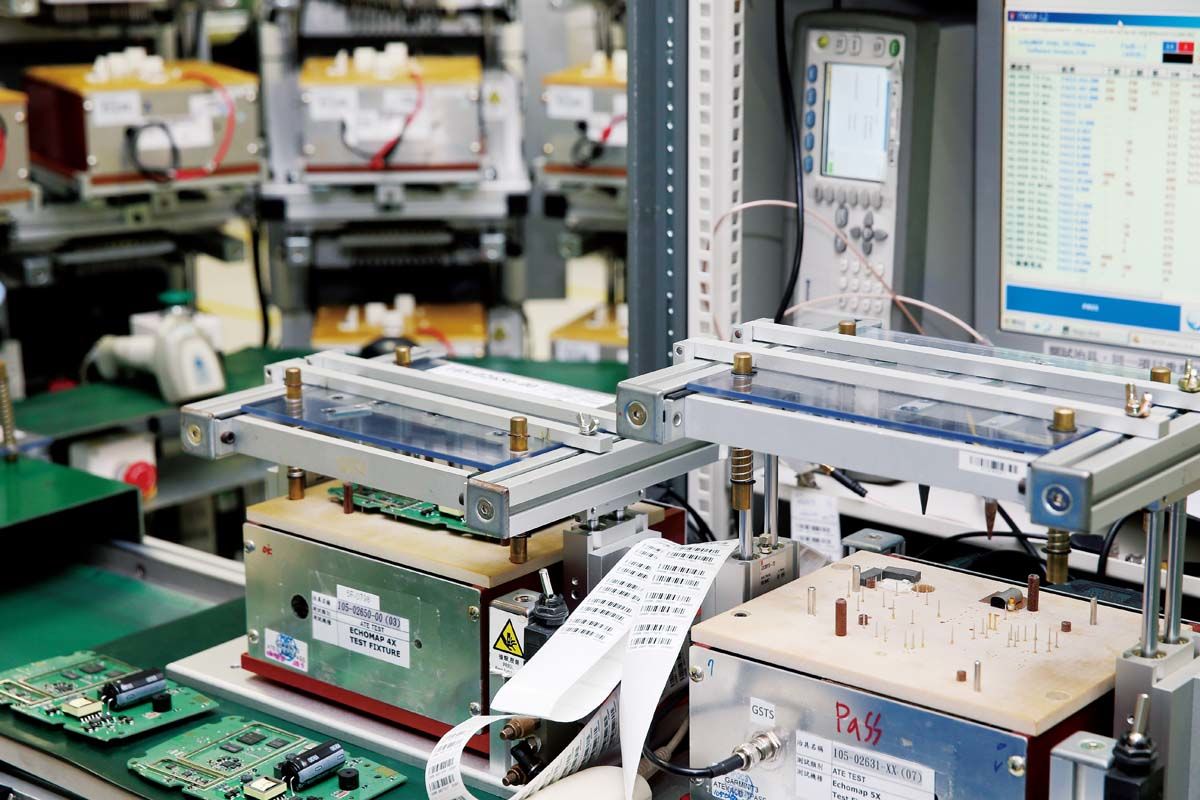 |
肉眼檢測一遍後,電路板便接上線由電腦接手,實際測試電壓和電流是否正常、藍牙有沒有連線以判定這塊電路板能否正常運作。 |
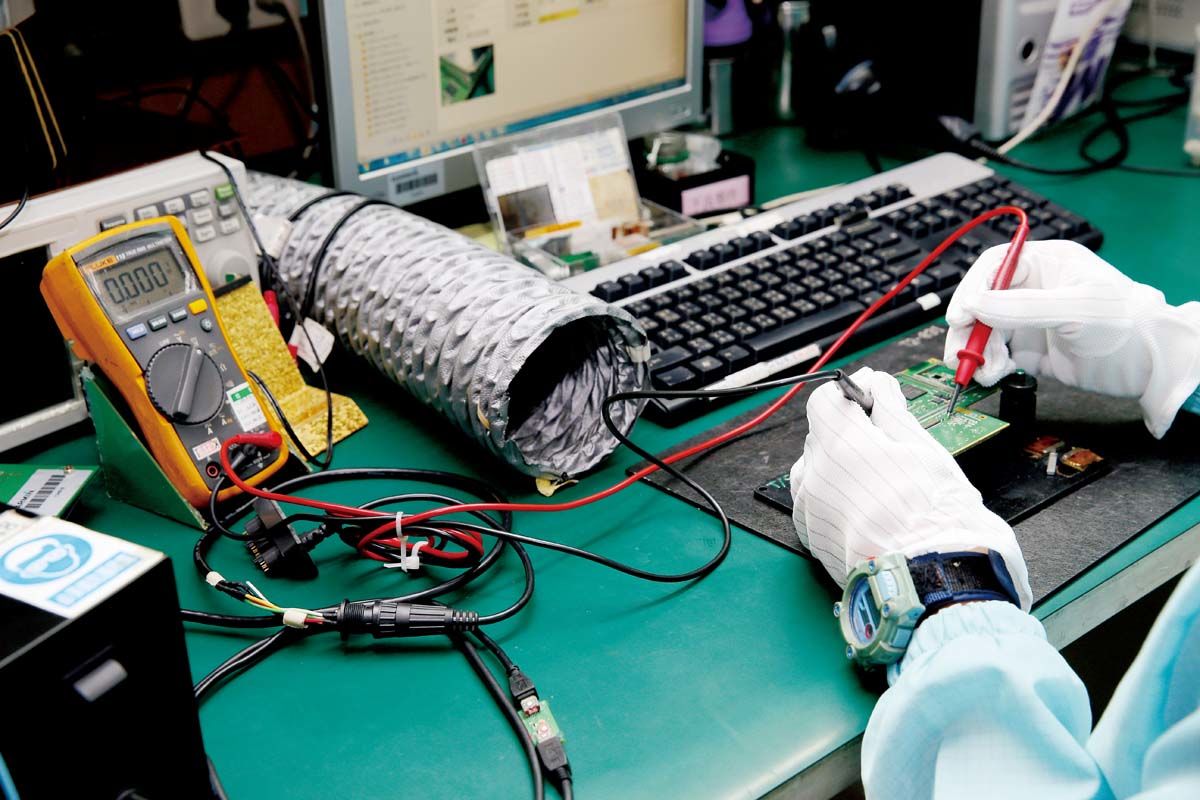 |
若是生產線旁無法簡易進行的維修,則必須送至專職的維修單位進行更仔細的檢查和修復。 PART 2各部位零件合體 導航機組裝大功告成 在一塊電路板妥善處理完畢之後,接下來就輪到導航機最繁瑣、最末端同時也最迅速的組裝線了。基本上Garmin從很早以前便已經安排身障工作者在這條生產線上處理這一系列讓導航機成形的動作,以配合政府鼓勵企業任用身障者的政策,並善盡回饋社會的一份心力。 |
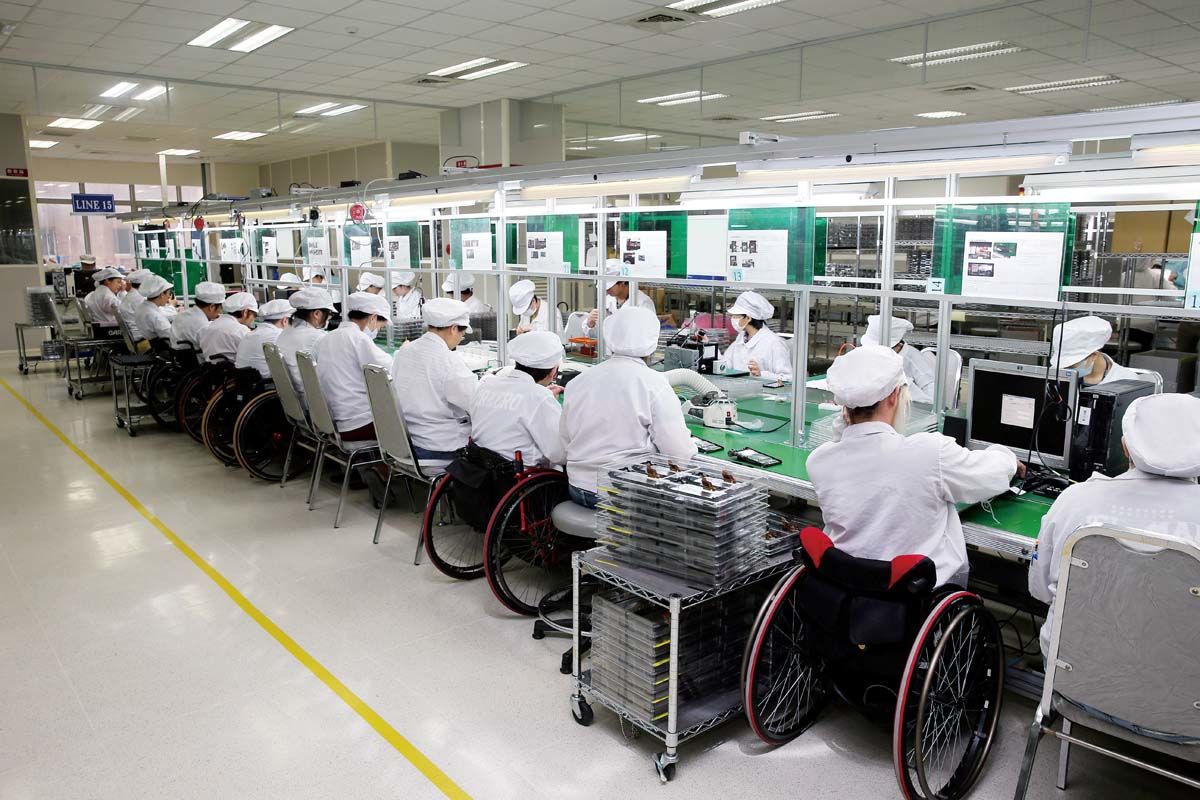 |
根據生產SOP規範 組裝可分為下列步驟 步驟1:導航機的組裝主要先將去除離型膜後將喇叭背膠放在冶具上,接著蓋上冶具放上喇叭、將喇叭放在對位冶具上,最後再放上後殼到對位冶具上並將開關鍵裝在後殼上。同時間電池件貼在後殼上以後接著透過壓床進行壓合,然後再將泡棉貼在後殼上,另外主板上貼上小鐵框和泡棉並放在流線上,然後再裝後殼側邊螺絲固定座,第三階段則是將鏡頭模組利用治具放在後殼上,並利用螺絲對角鎖緊。 |
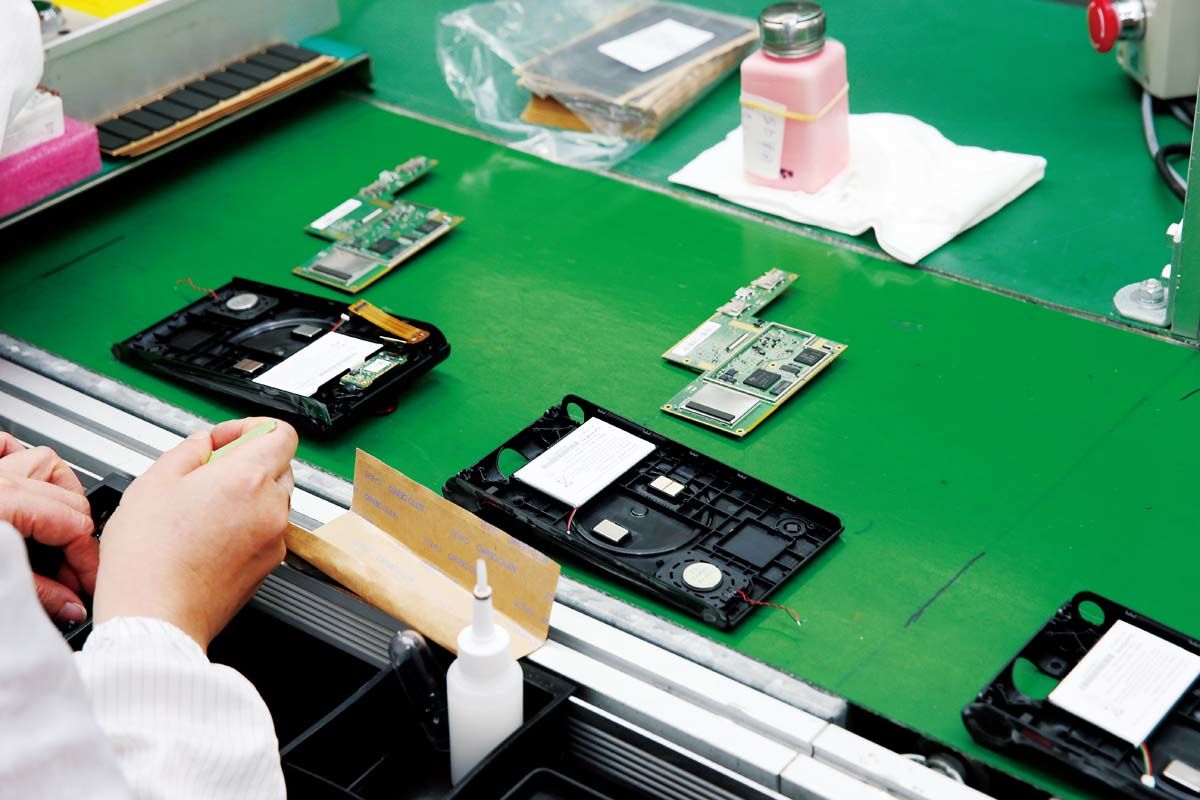 |
步驟2:接著比較重要的就是條碼安裝,先將後殼放在冶具上並且鎖上螺絲、扣上軟排線、安裝麥克風後,再利用條碼編輯程式輸入工單號碼,接著將電池和主板序號刷入,這個程序同樣能夠確保這兩件重要部件確實編號並利於品質管理上的控管追蹤。錄影按鍵和相關軟排線隨後在第六關步驟安裝在後殼上,同時工程人員還必須先行測試錄影按鍵的手感。 |
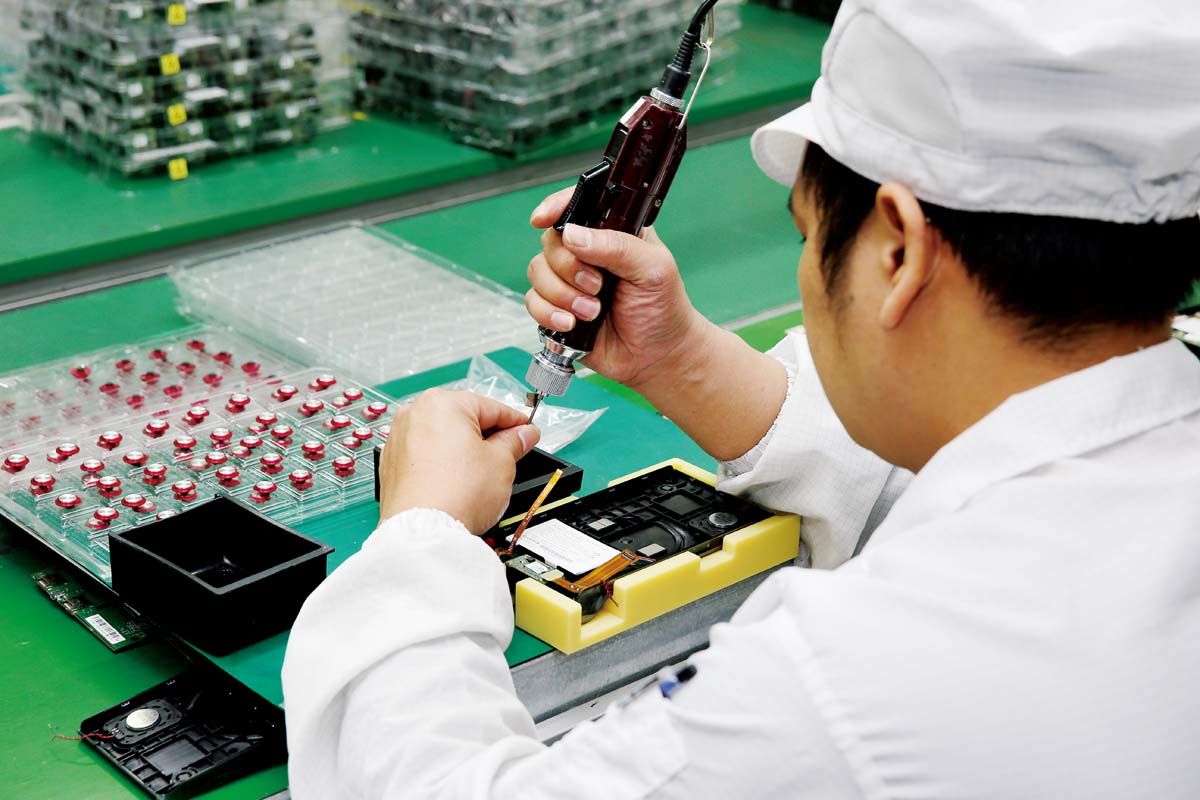 |
步驟3:先將鏡頭軟排接到主板上,接著再將主板安裝在後殼上,同時記得將電池線和麥克風線先行拉出,接著再插錄影鍵軟排,最後以對角將螺絲鎖在主板上,並將按鍵軟排的線材所在鏡頭板上。檢查鐵蓋是否貼上泡棉後將大鐵蓋裝上機台,接著貼附錄影按鍵的軟排泡棉,以及取兩塊短導電泡棉至板子上。 |
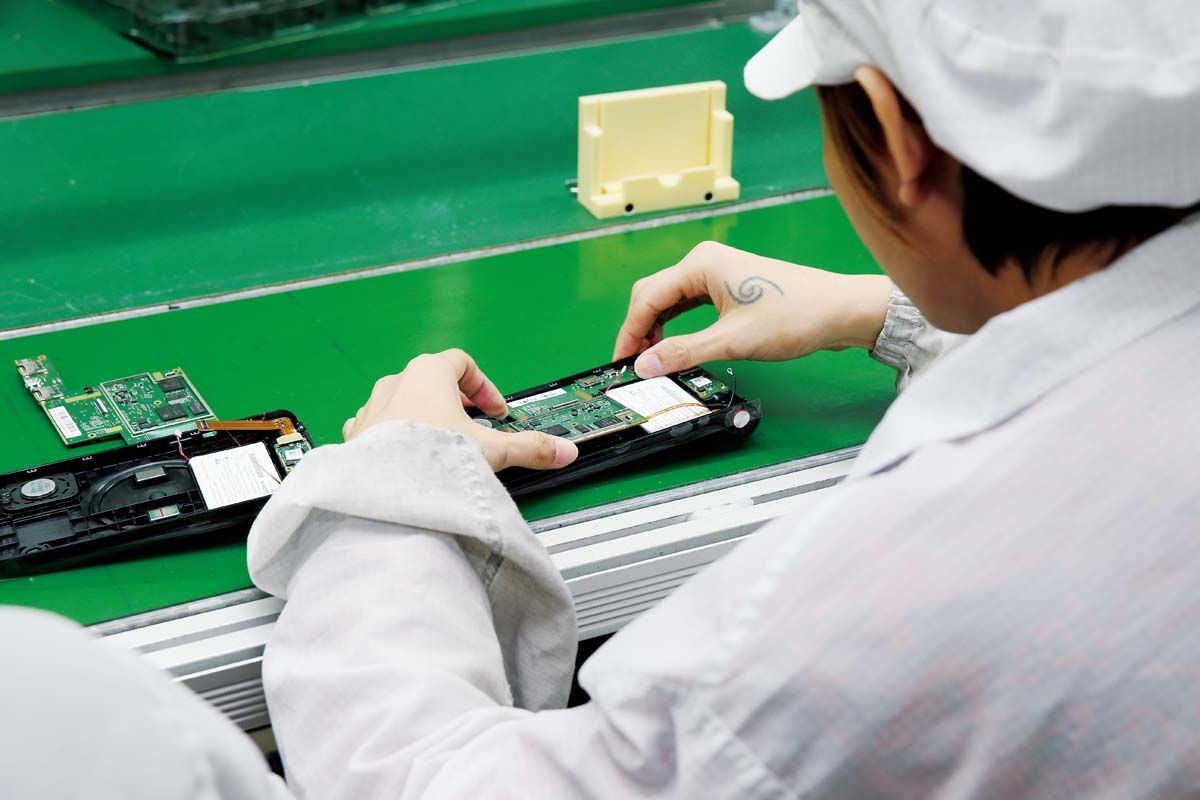 |
步驟4:這個流程就輪到人工焊接的技術登場了,分別是焊接一組後殼麥克風、喇叭並貼附一顆導電泡棉。焊接完成後,使用綠色膠帶固定鏡頭軟排,貼完後還要轉動鏡頭檢查是否會有異音發出。 |
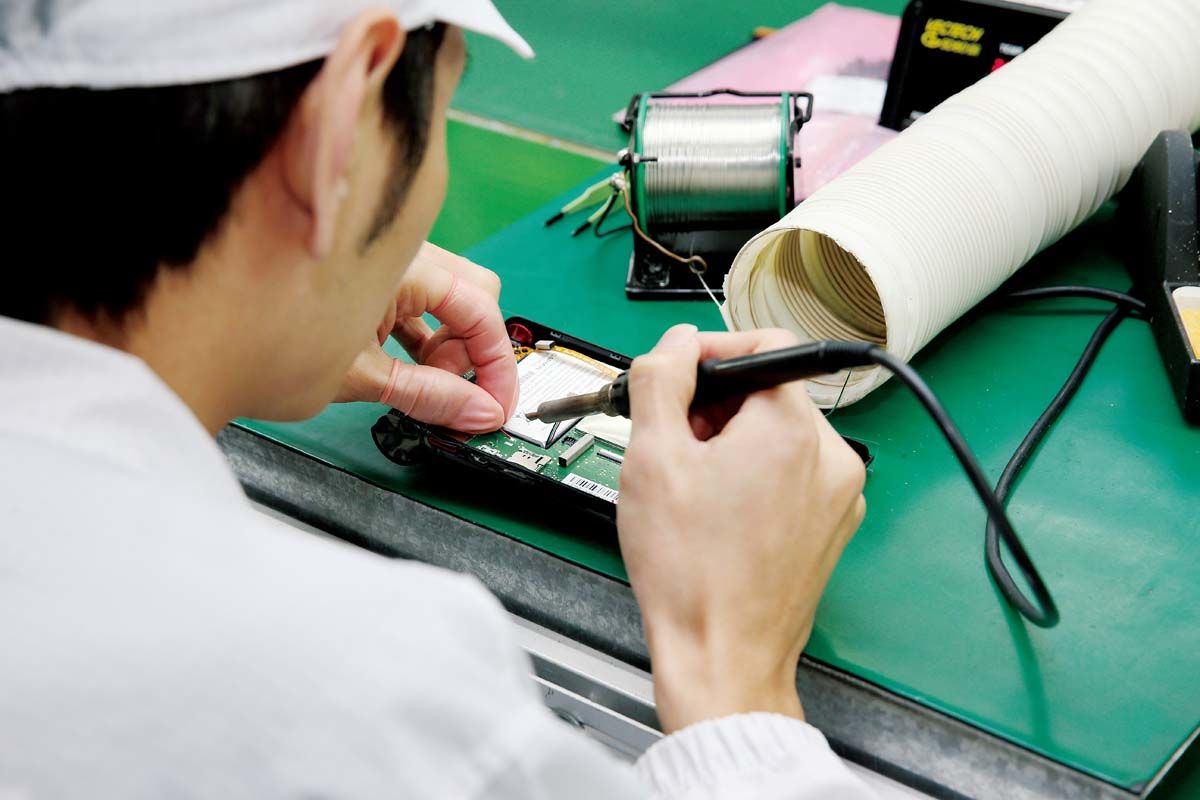 |
步驟5:將顯示螢幕軟排接到主機板上,接著插上USB連接至機台上讓電腦讀取主機板序號,在這個程序上還必須刷鏡頭條碼並檢查顯示螢幕畫面是否正常。最後再將機台直立,並將前殼麥克風塞進前殼,然後以膠帶固定麥克風線並蓋上前後殼。 |
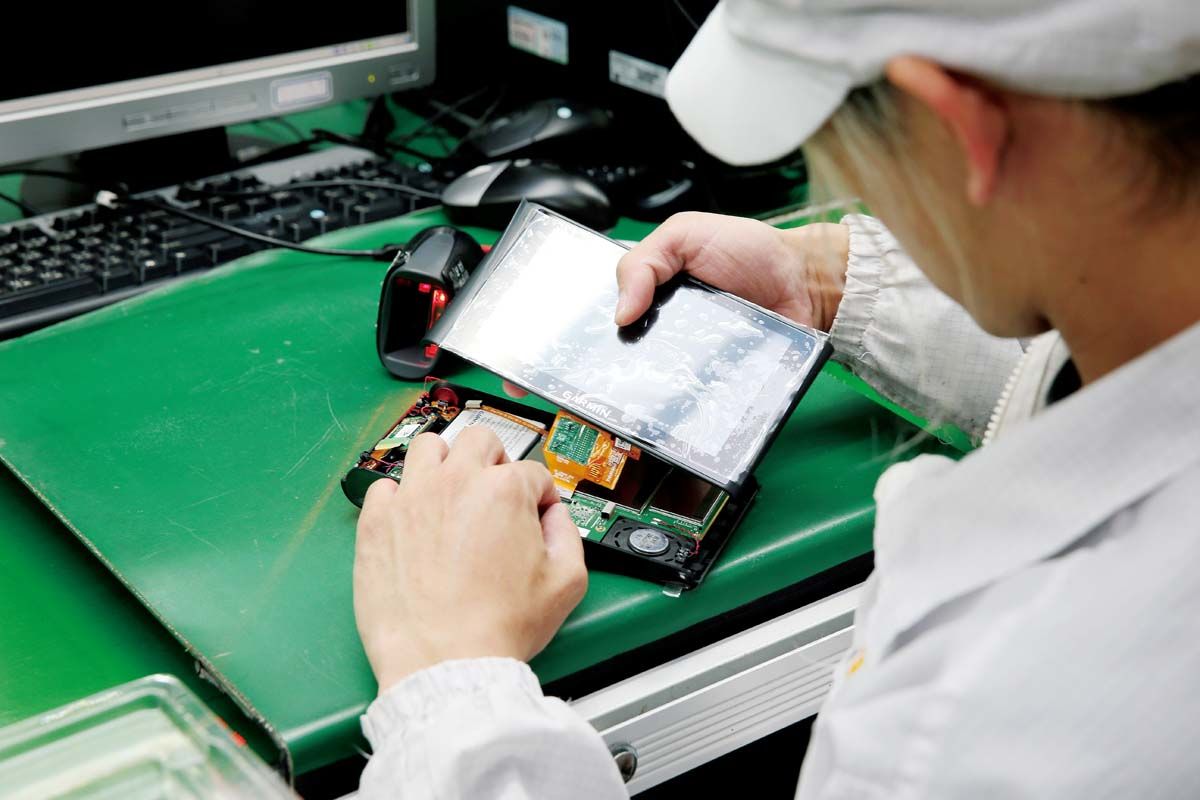 |
步驟6:最終一站就是輸入工單號碼,並利用程式進行測試,檢查機台螢幕、GPS和喇叭音量是否正常,並且以100克壓力筆檢查螢幕有無水波紋。若碰到問題,就按照先前程序一樣交付給檢修人員進行檢查,並進行初步維修。若一切運作順利,便可傳送至下一階段進行冷、熱測試,考驗導航機的耐用度。 |
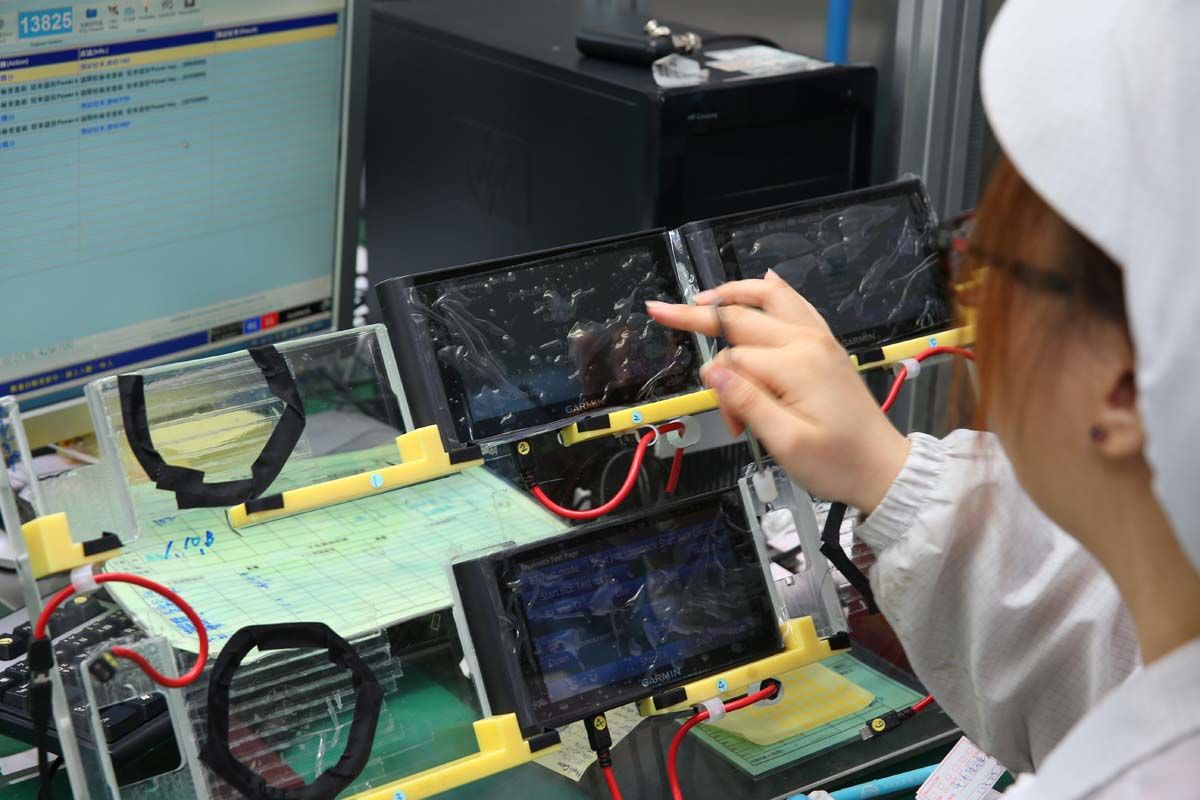 |
加工觸控螢幕的超機密無塵室 目前從導航機到行動電話都以結合觸控面板的全彩顯示螢幕為主軸,觸控面板和平面顯示器這兩種高科技產品通常像Garmin這樣的大廠都是透過代工廠代工,而無塵室中的工程人員主要是針對以上兩項主件進行加工接合的動作,結合完畢再送出無塵室進行觸控介面操作測試。 |
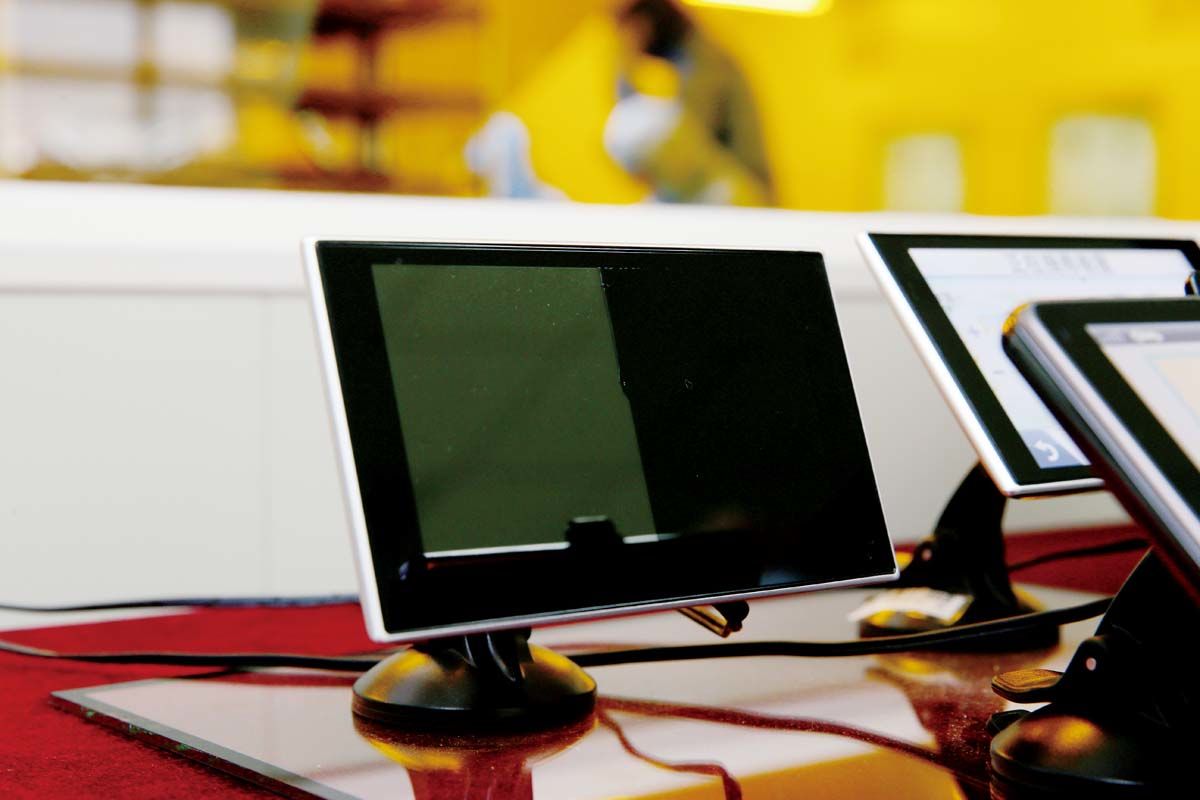 |
右半部進行全貼合和左半部只做口字型貼合的螢幕呈現,有著觸控品質、是否產生疊影和畫質上的明顯差別。 目前新的導航產品以經過全貼合的觸控螢幕為最具競爭性,所謂的全貼合,就是觸控面板與平面顯示器以透明光學膠進行黏合動作,並以完全貼合的方式讓兩層板之間完全密合而沒有任何空氣。這種貼合方式比起一般口字膠貼合,不會有光線折射產生疊影的缺點,同時還能呈現高彩度品質,厚度也降低許多。而由於我們在無塵室內進行貼合工作,因此過程中螢幕也不會有灰塵竄入,而化學膠的優點更讓觸控訊號不會受到顯示面板雜訊的干擾,不過成本自然要比口字膠貼合來得高。 全貼合的動作簡單來說就是先以貼合機將OCR液態光學膠黏附在玻璃上並對位壓合,且讓膠均勻擴展到全平面,接著再以UV光將光學膠全面固化。雖然說程序看來簡單,但導航機要做到彩度良好、又不會因為光線折射影響畫面呈現,中間還是加了許多屬於內部機密的步驟,基於保護的理由,在此我們不便公開。 |
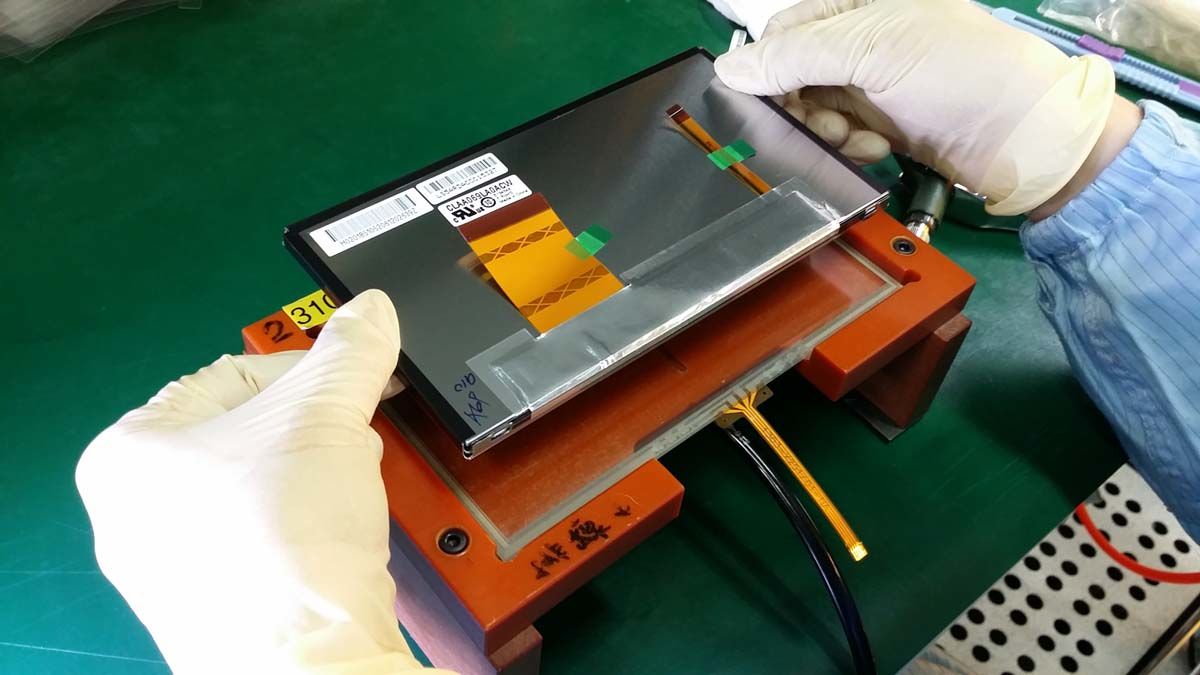 |
觸控顯示螢幕的構造主要由玻璃屏幕、結合軟性印刷電路板的觸控面板、偏光板和顯示面板所組成,末端則結合顯示驅動積體電路。 |
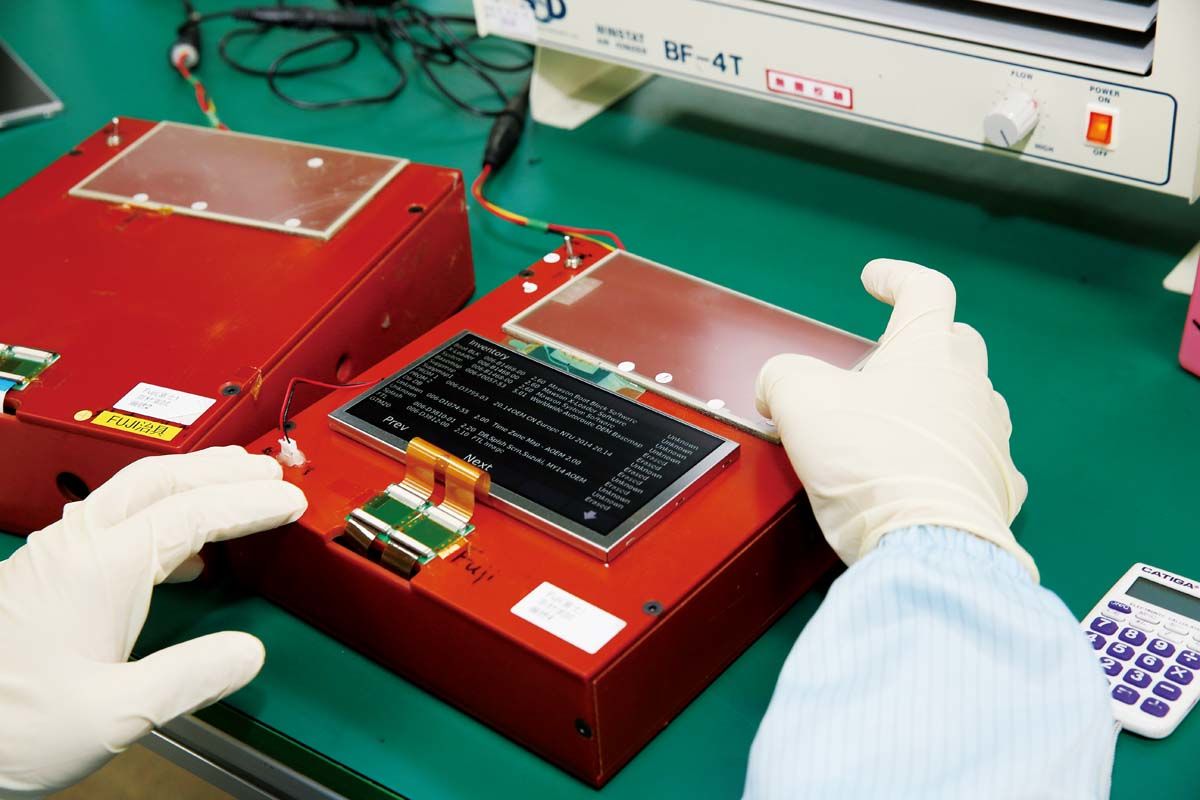 |
結合完畢後,觸控顯示螢幕則交由測試人員進行操作測試。 小盒子竟暗藏這麼多科技知識 雖然導航機問世了那麼久,我們或多或少也曾經透過各種節目介紹得知導航機運作原理,但頭一次進入生產線上看清楚這個小盒子的各種秘密卻是頭一遭,從最原始的印刷電路板、路調車所傳回的資料中每張環景圖和每個座標點附近的資訊轉換成地圖檔、極精密且機密的觸控螢幕加工、導航機整體裝配及最後測試,看似簡單的電子產品組裝卻暗藏眾多標準流程和獨門技術,我們才能在車上使用怎麼樣都曬不壞的高品質導航機器。 |
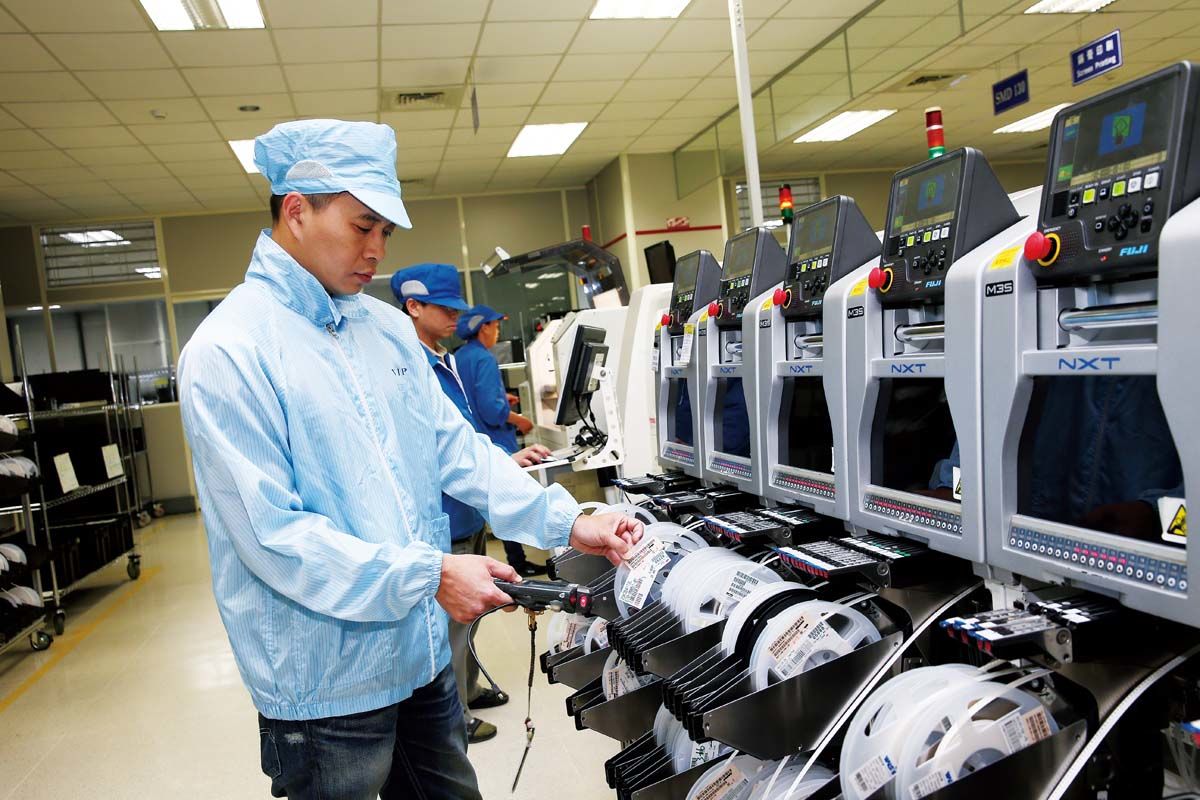 |
冷脹熱縮還操不壞 |
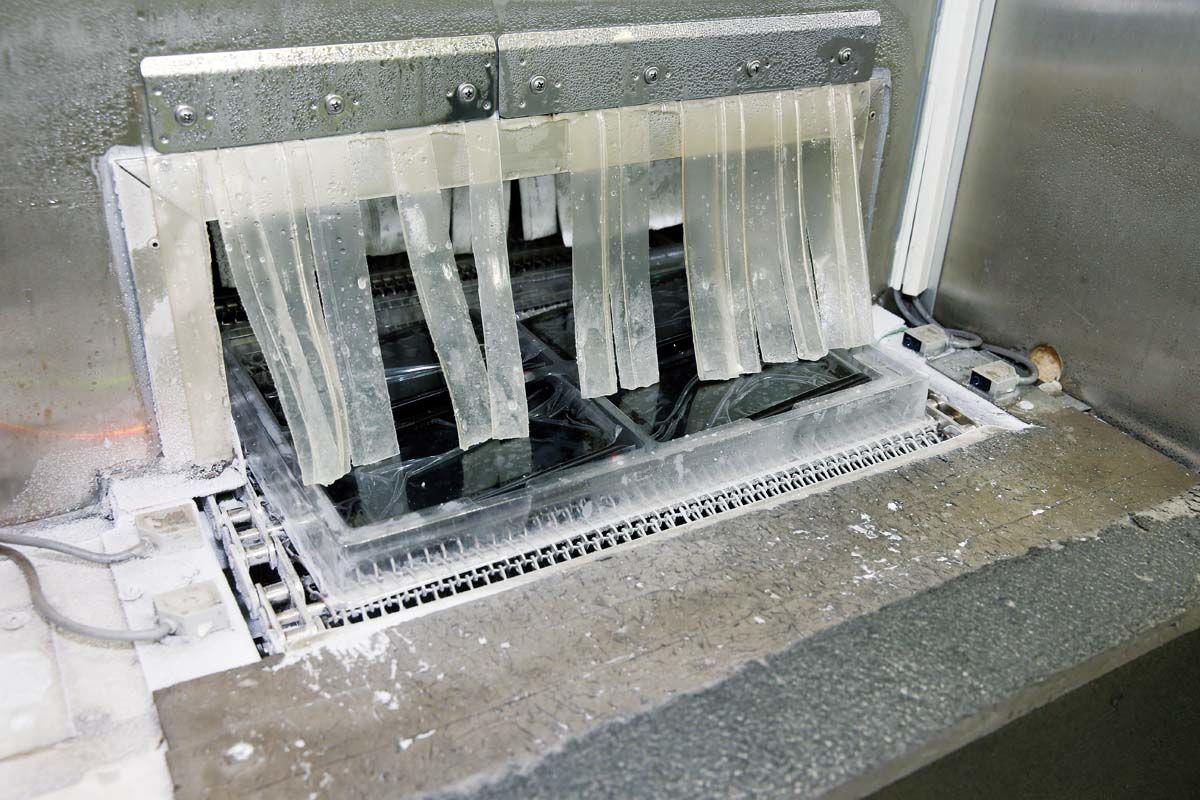 |
安排在生產線上的低溫和高溫測試機台主要分別透過攝氏零下負20度和 約60度的高低溫考驗,經過冷縮熱脹的程序後便進行最終測試,最後的測試流程能夠讓導航機內所有組裝不良的現象一一現形,透過導航系統內各功能選項的操 作、螢幕的觸控、GPS的接收感度、音源的輸出到相機運作效果,在察看無誤後確保產品在品質規範內,最後才能推出市場販售。 |
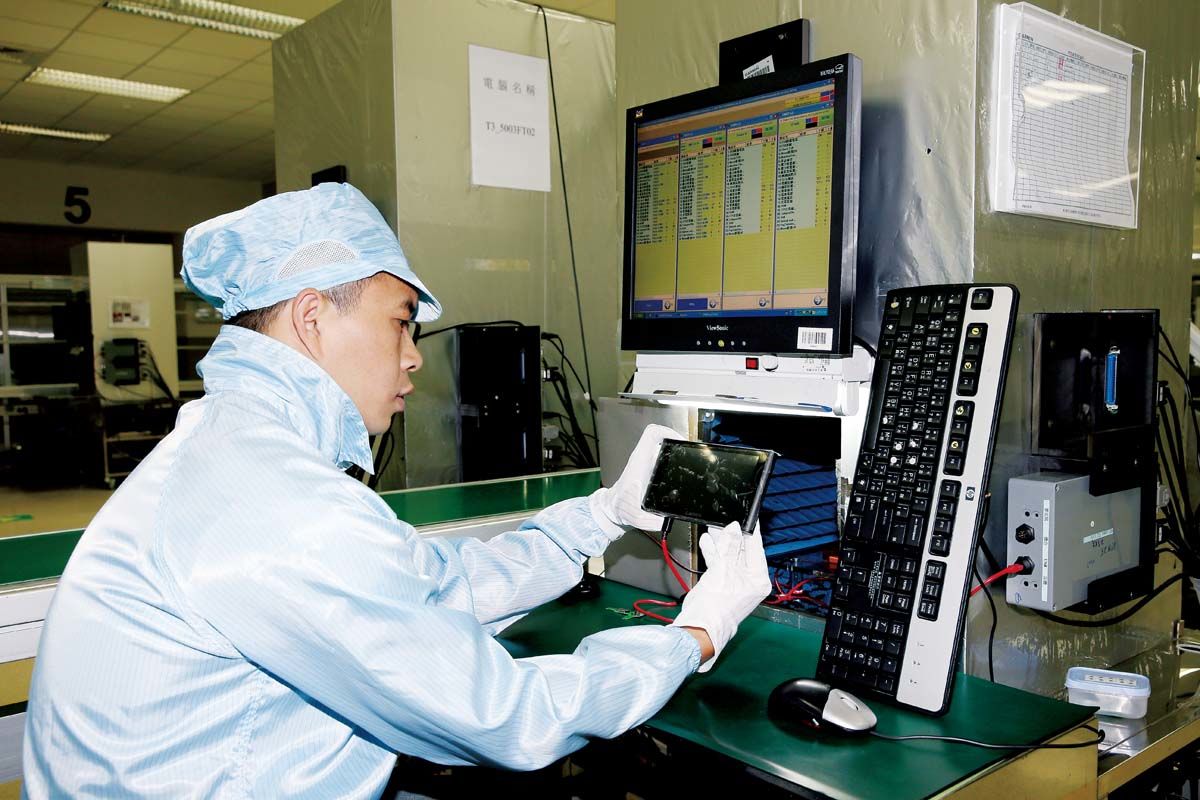 |
待導航機解凍後隨即進行測試,透過各種功能的操作,若有組裝線上的瑕疵就會透過故障問題一一呈現。 |